Our Heritage
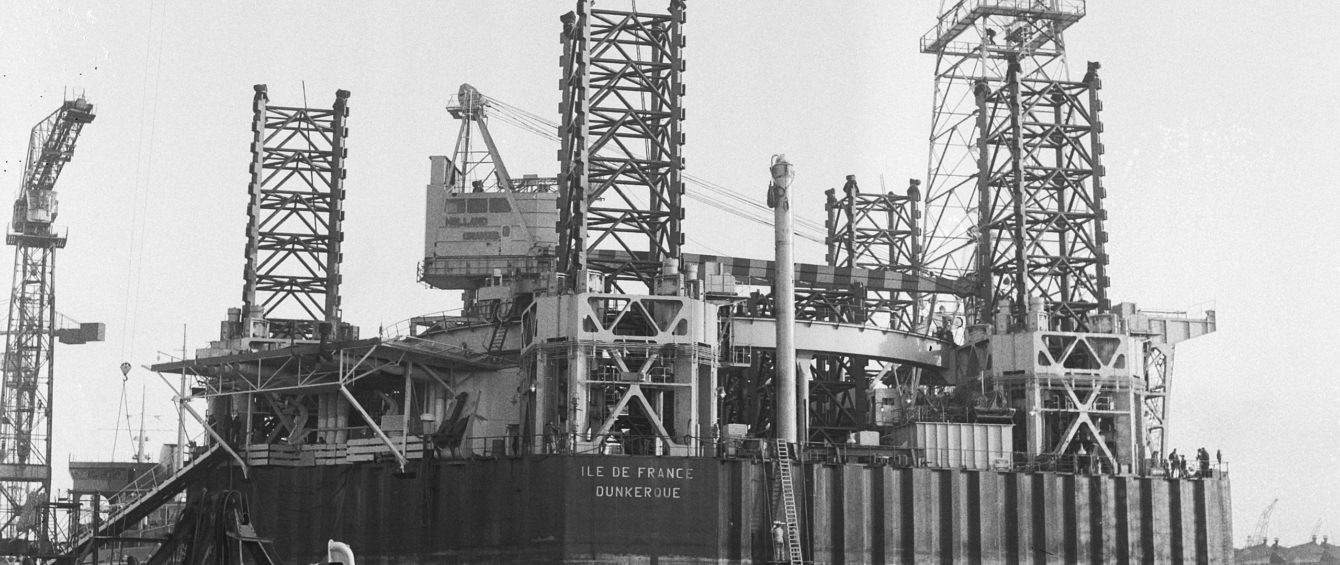
2024
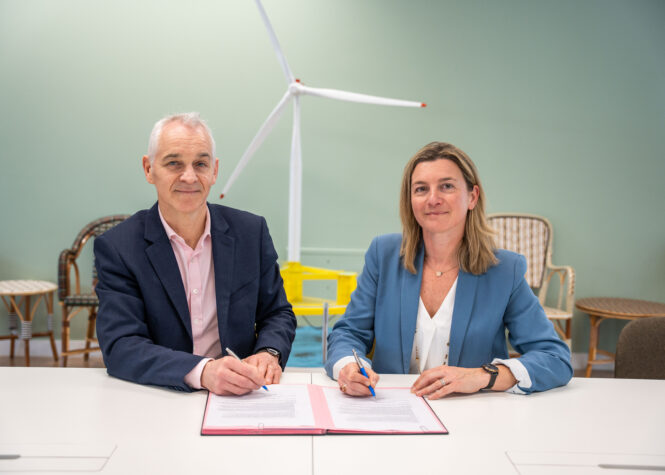
Creation of Ekwil J.V. with Technip Energies for Floating Offshore Wind
2024
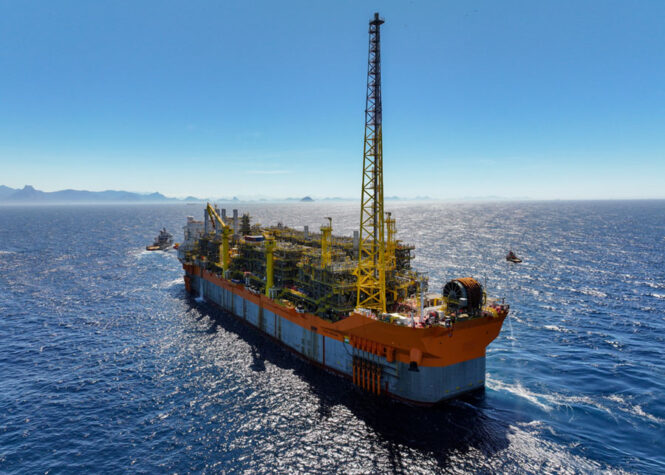
The first F4W FPSO Sepetiba arrives in Brazil
2024
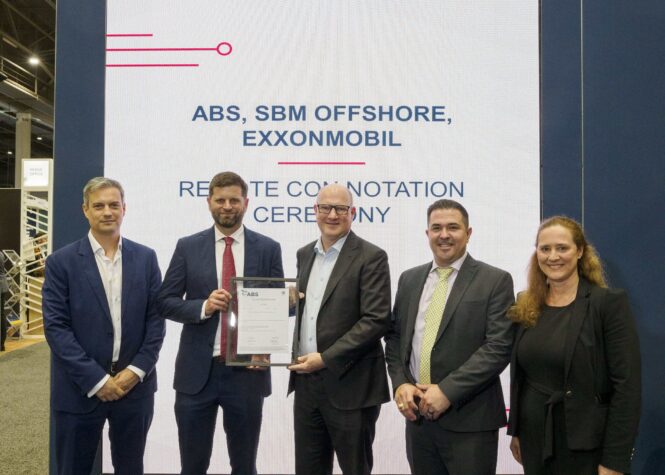
First FPSO with ABS REMOTE-CON Notation
2023
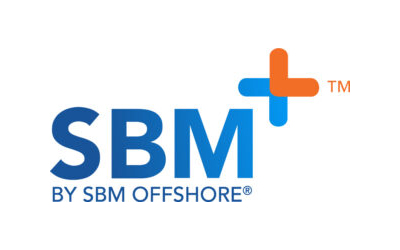
Launch of SBM+ – digital solutions platform
2023
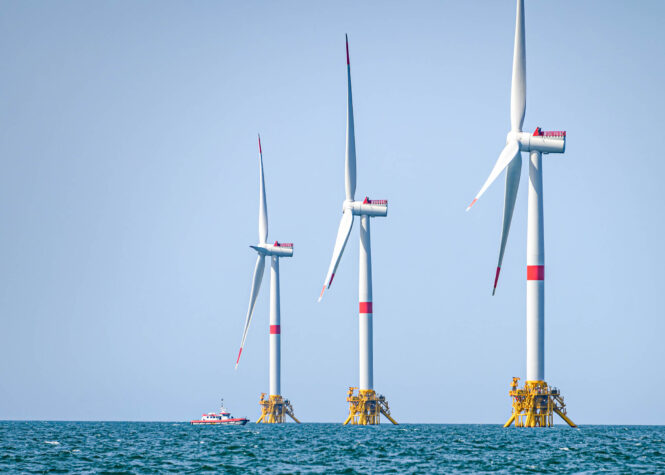
Delivery of first pilot Floating Offshore Wind farm, Provence Grand Large for EDF
2023
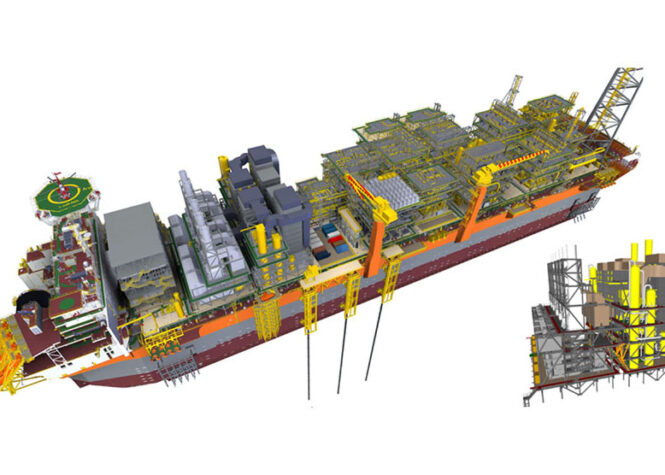
FPSO Carbon Capture module qualified by DNV
2023
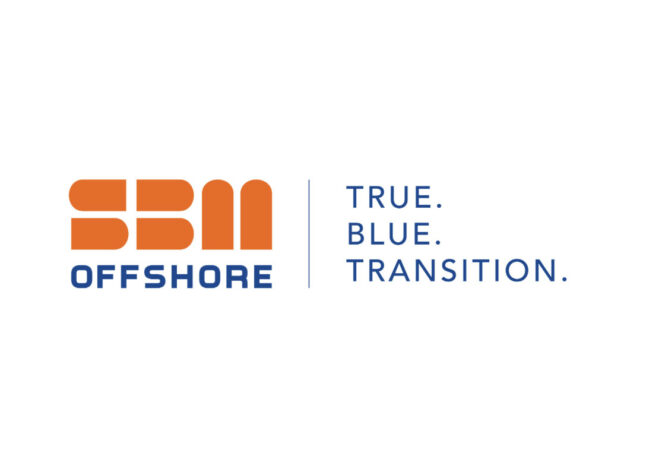
SBM OFFSHORE embraces the TRUE. BLUE. TRANSITION.
2022
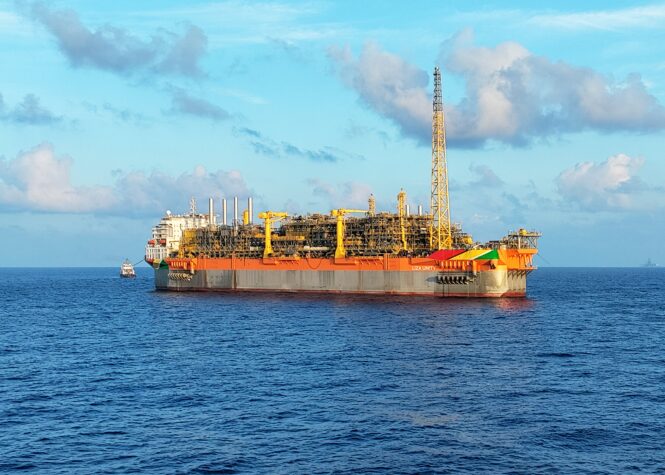
First Oil from 1st Fast4Ward® FPSO
2022
Ammonia CALM buoy receives AiP from DNV
2021
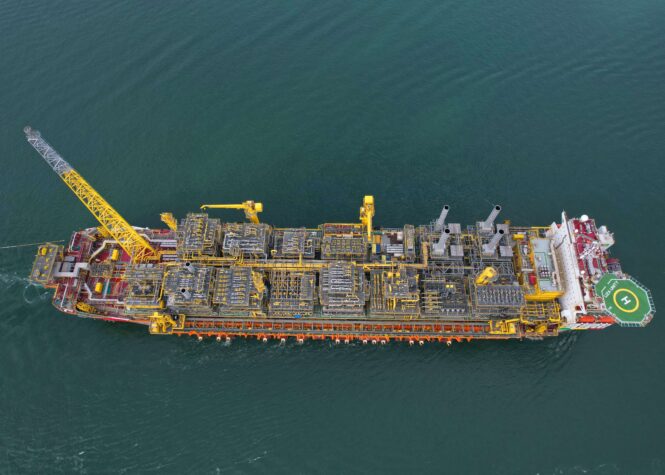
First FPSO with ABS Sustain-1 Notation
2021
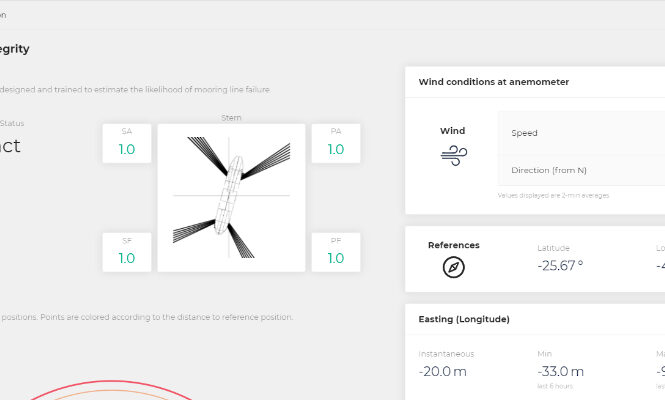
Intelligent Agent Mooring Line Integrity Tool qualified by ABS
2021
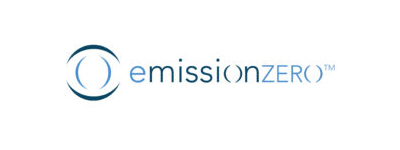
Launch of SBM Offshore’s emissionZERO® program
The program targets floating energy production solutions with near zero emissions
2020
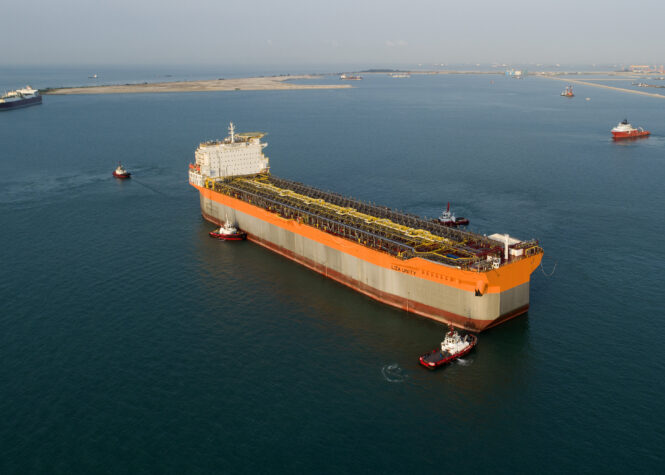
First completed Fast4Ward® hull
The hull for Liza Unity FPSO project arrives in Singapore for its topsides integration.
2019
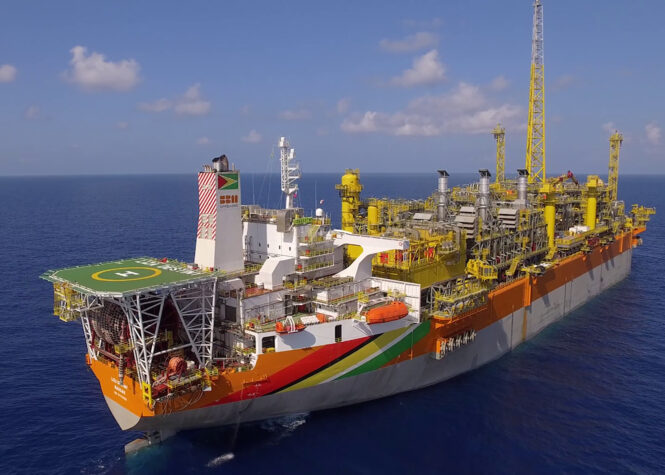
Liza Destiny FPSO is installed offshore Guyana
Making it the first installation for oil and gas production in the country
2018
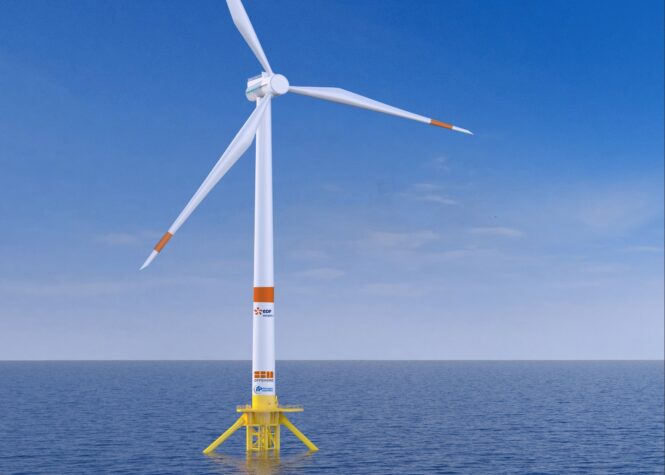
SBM Offshore moves into the renewable energy sector
With the launch of the Wind Floater program
2016
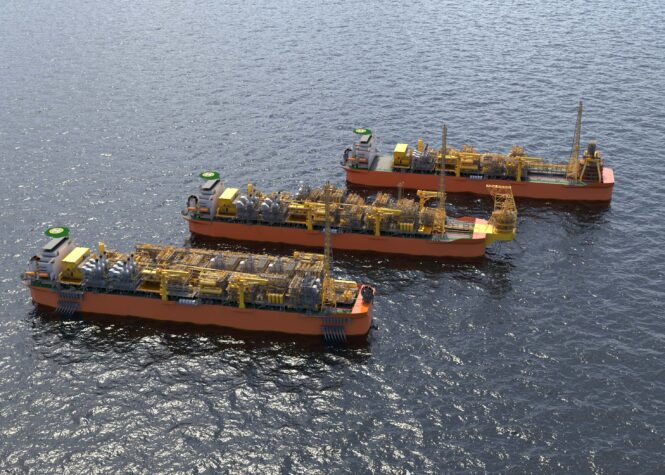
SBM Offshore launches the Fast4Ward® Program
Leveraging standardized designs for construction of Multi-Purpose Floater hulls and topsides. With this program, SBM Offshore can deliver the product to clients faster and at lower cost, industrializing the FPSO business.
2016
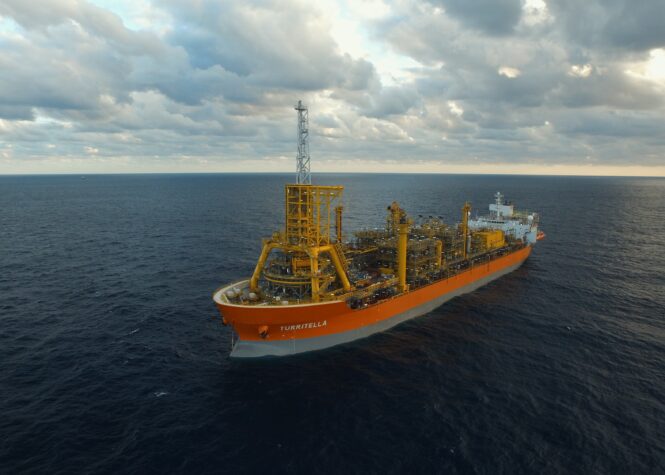
FPSO Turritella is installed in the Gulf of Mexico
Making it the world’s deepest moored unit
2013
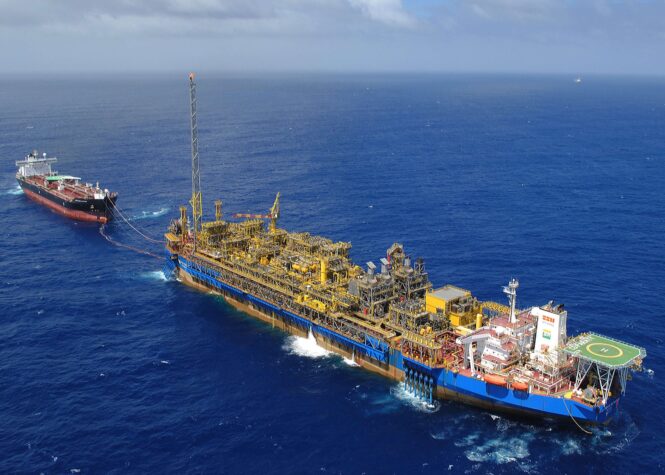
Generation 3 FPSO enters the market
2013
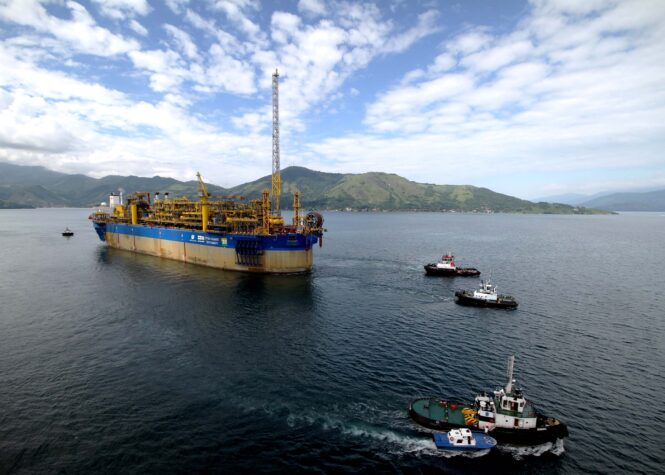
FPSO Cidade de Paraty (Brazil)
FPSO Cidade de Paraty was constructed in line with expectations in 34 months from the signing of the Letter of Intent in June 2010 and meets local content requirements for Brazilian FPSOs. The FPSO will operate under a twenty year charter and operate contract on the Lula Nordeste development in the pre-salt area, offshore Brazil.
2013
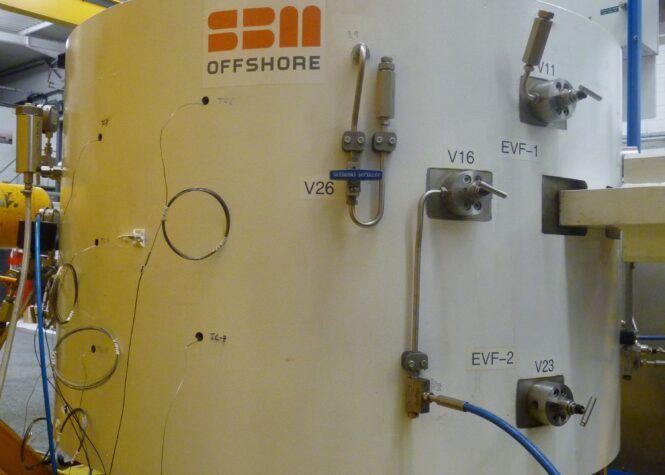
VHP Swivel rated at over 800 bar
2012
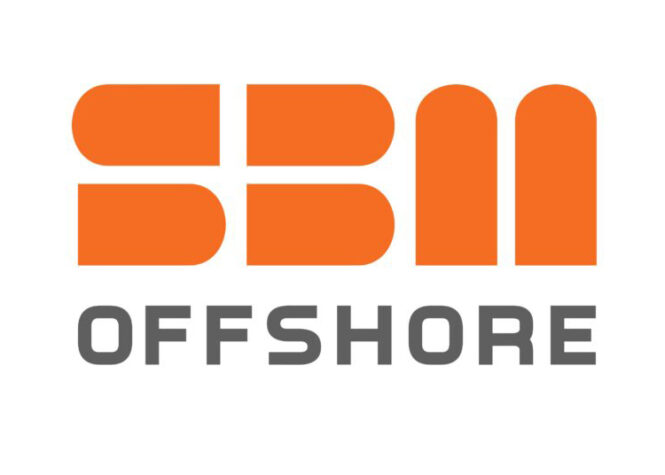
New SBM Offshore Brand
SBM Offshore decided to change its business for good to strengthen its position as a global leader in floating production and mooring systems, in production operation, and in terminals and services.
2011
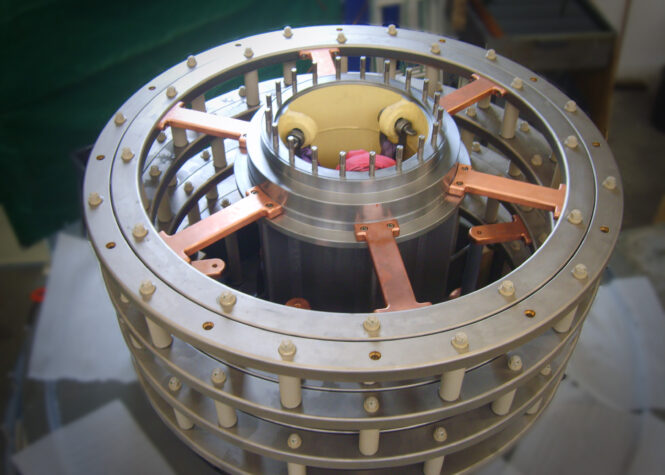
Qualification of the AC High Voltage Swivel
SBM Offshore’s design for a High Voltage Swivel design was qualified. It is suitable for around 150 MW capacity and will allow large FPSOs to be fully powered from shore.
2011
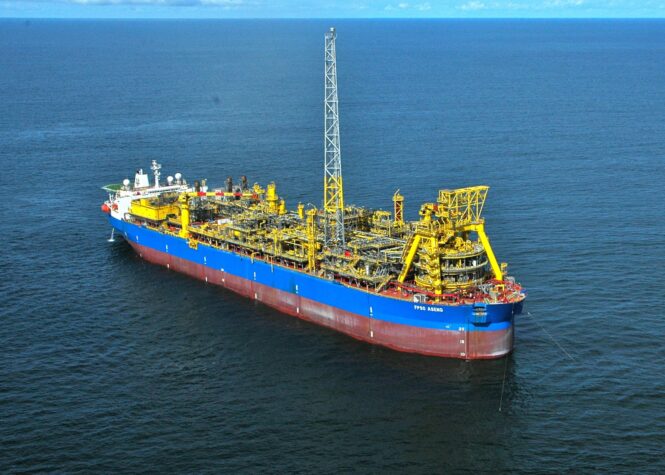
FPSO Aseng – FPSO supplied in record time
This FPSO project was delivered two months ahead of schedule and was delivered only two years after contract award. The Aseng FPSO has processing capacity for 120,000 barrels of liquids per day, including 80,000 barrels of oil and can handle 170 million standard cubic feet of gas per day. The unit has storage capacity for 1.6 million barrels.
2011
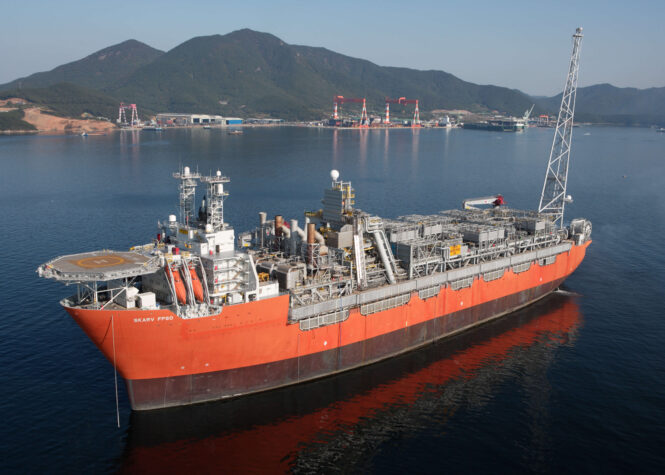
5,500 Ton Turret for Skarv FPSO
The internal turret, based on the bogie-bearing design, was installed on the Skarv FPSO owned by BP and represented one of the largest and most complex turrets ever built by SBM Offshore. The FPSO is on location in the Skarv field offshore Norway.
2011
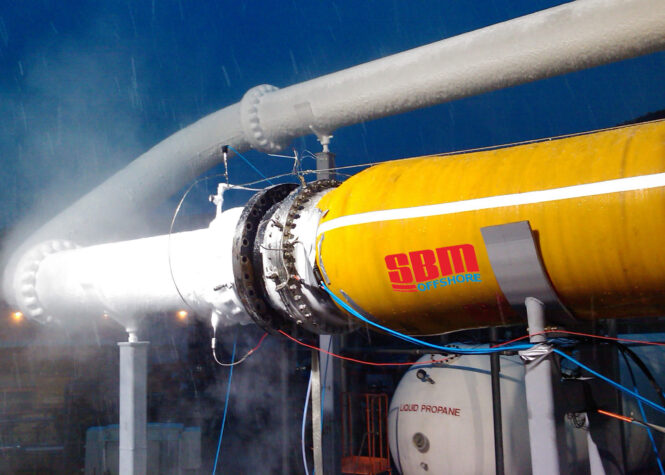
COOL™ LNG Transfer System
The COOL™ was the industry’s first fully qualified and certified floating offshore LNG transfer system. It represented a step change in the safe and reliable transfer of Liquified Natural Gas in tandem configuration.
2010
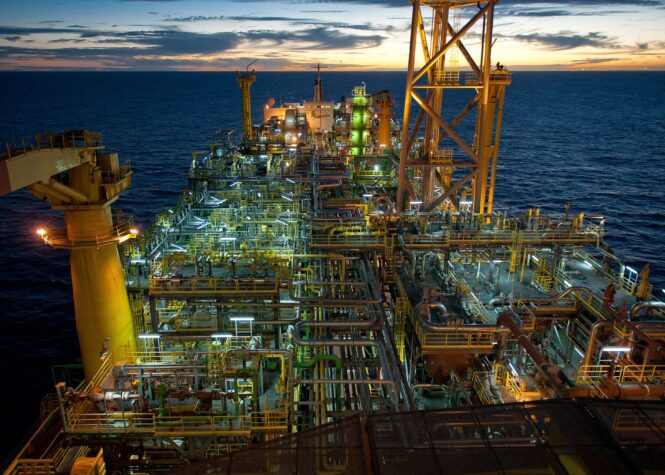
+3 billion barrels produced oil & 200 years cumulative operating experience
SBM Offshore has the largest global floating production fleet to date. In 2010, we celebrated over 200 years of cumulative operating experience, over 3 billion barrels of oil produced through our units, and over 5,000 offloads. The fleet had an uptime average of 99%.
2010
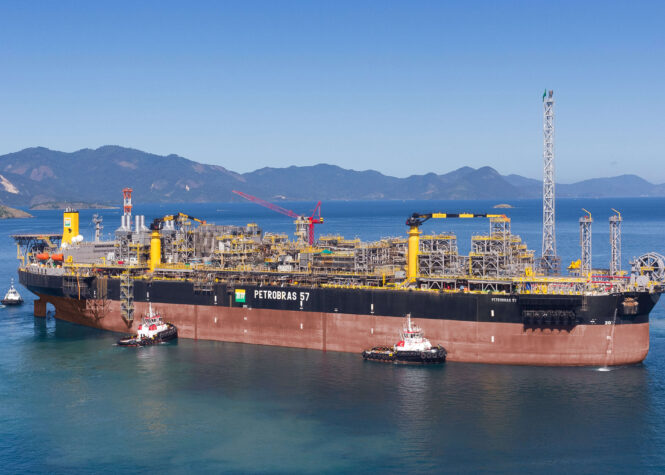
Largest Turnkey FPSO with 65% Local Content for Brazil
P-57 was the 8th Brazilian FPSO that SBM Offshore delivered and was the largest to date. Delivered ahead of schedule, it was the first contractor designed and supplied FPSO built with 65% local content.
2009
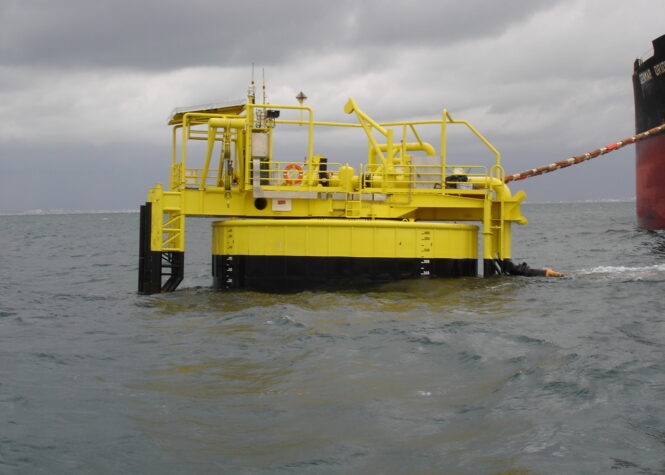
50th Anniversary of the CALM Buoy
SBM’s introduction of the CALM Buoy in 1959 was the beginning of a technological revolution in the offshore oil and gas industry. Single Point Mooring (SPM) technology is now the standard in the loading and offloading of hydrocarbons.
2008
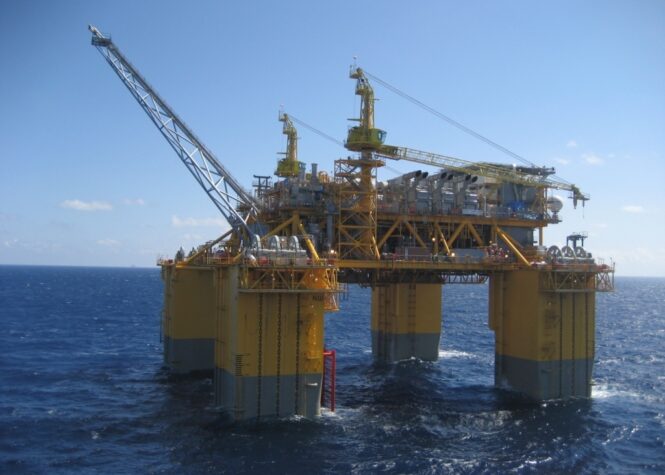
First DeepDraft Semi with PHA Contract
Murphy Oil contracts for the five-year lease of a newbuild semisubmersible floating production unit for the development of the Thunder Hawk field offshore Louisiana in the Gulf of Mexico.
2008
First Turret-Moored FPSO with SCRs
FPSO Espirito Santo is hooked up to the mooring lines in the BC-10 field offshore Brazil. It was the deepest moored FPSO of the company’s fleet and the first turret-moored FPSO in the world to use steel catenary risers for fluid transfers.
2007
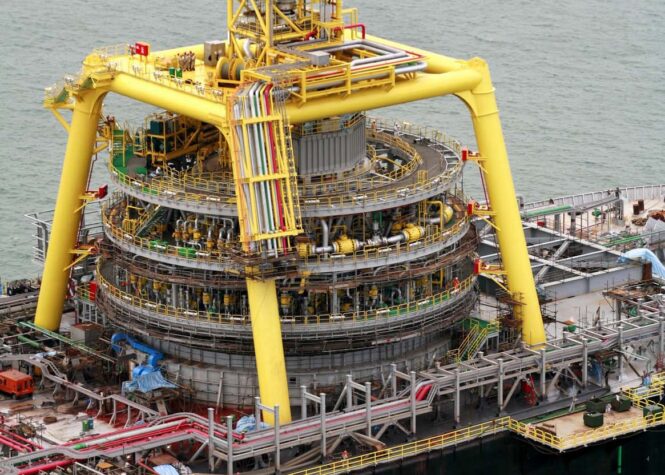
Largest Internal Turret
The internal turret mooring with 75 risers for FPSO P-53 for the Marlin Leste field offshore Brazil is completed and delivered to Petrobras.
2007
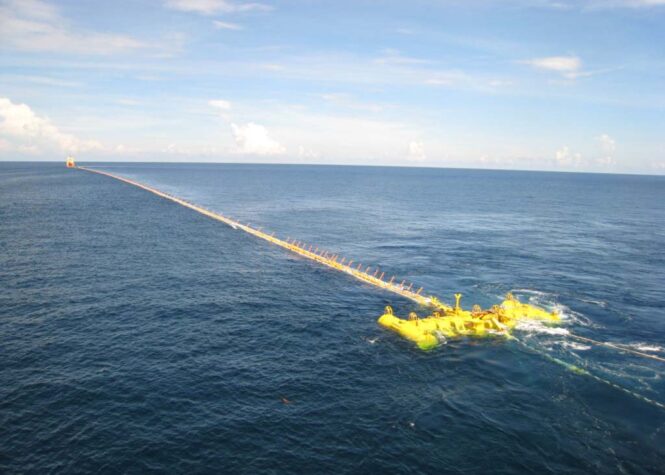
FTL-GAP™ Fluid Transfer System
Installation, hookup and commissioning of the Gravity Actuated Pipe (GAP™) system is completed for the transfer of producing wells on the Kikeh field, offshore Malaysia.
2006
Kuala Lumpur Execution Center Opens
SBM Offshore opens an execution center in Kuala Lumpur, Malaysia. This center increases the capacity of the company to execute large and complex projects.
2006
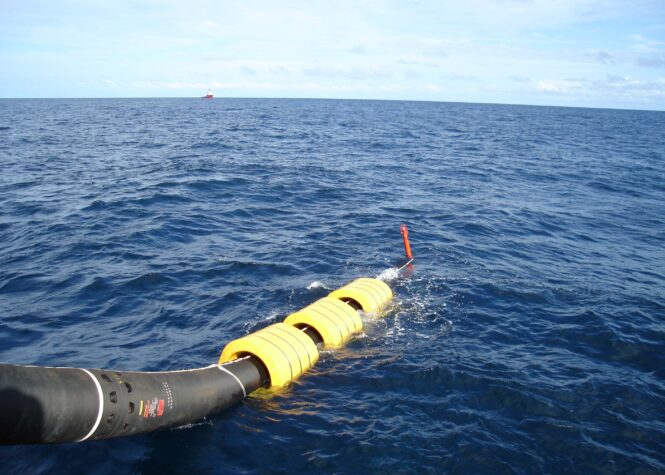
Offshore Offloading Line Installed
The supply and installation of a Trelline™ flexible export line at Shell Nigeria’s Bonga field is successfully completed.
2006
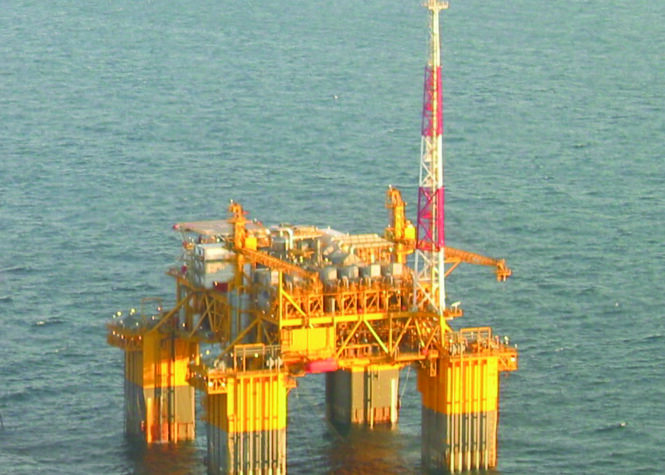
Deepest Semisubmersible
The industry-first DeepDraft Semisubmersible is installed in a world-record 8,000 ft (2,438 m) water depth on the Independence Hub in the Gulf of Mexico.
2005
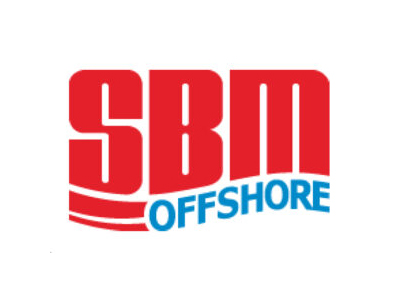
IHC Caland Becomes SBM Offshore N.V.
IHC Caland is renamed SBM Offshore N.V. The market downturn in the specialized shipbuilding market post-2000 and the financial imbalance and lack of synergy between shipbuilding and offshore oil and gas-related activities within the Group necessitate the divestiture of the Group’s shipyards beginning in 2003. By early 2005, all shipyards are sold.
2003
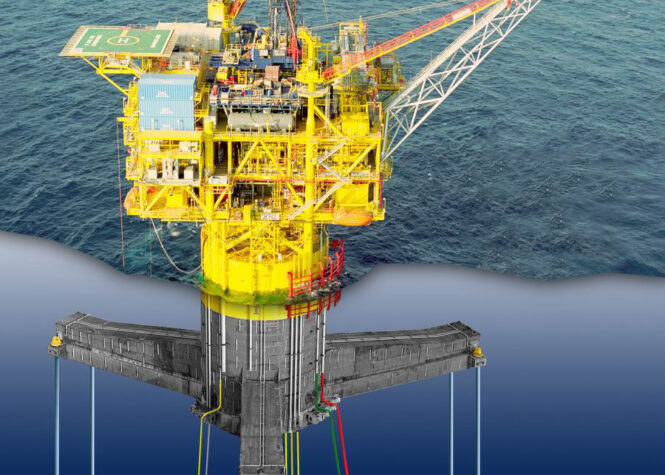
Largest Sea Star® TLP delivered
Delivery of the fourth and largest SeaStar® to Total for installation on the Matterhorn field in the Gulf of Mexico.
2002
Acquisition of Ocean Design Associates, Inc.
The Group acquires Ocean Design Associates (ODA), Inc. of Houston.
2002
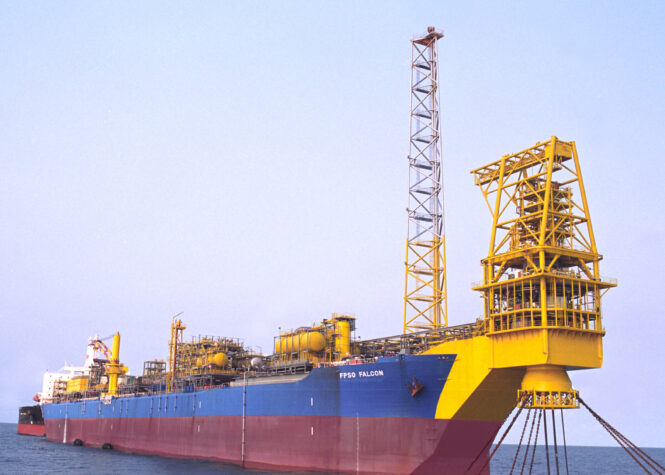
First Generic FPSO
ExxonMobil adopts the approach of leasing FPSOs and develops the generic FPSO concept. SBM wins the first contract with four more following.
2001
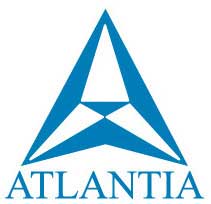
Acquisition of Atlantia
The Group acquires Atlantia Offshore, a company that specialized in the design and construction of tension leg platforms (TLPs). This strategic move successfully complemented the Group’s range of products while providing all building blocks needed for large deepwater oil and gas developments.
1998
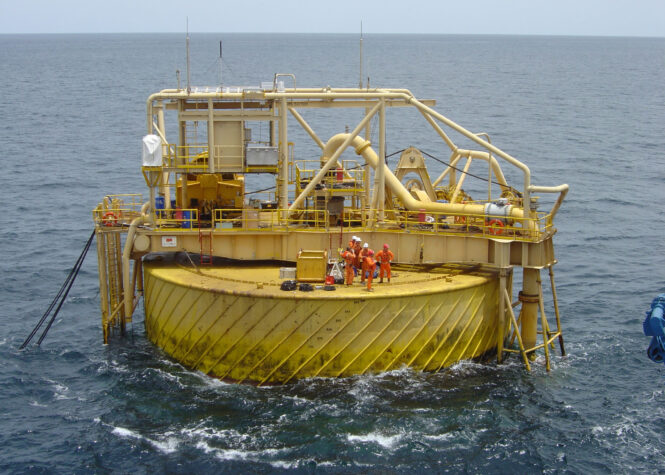
Deepwater CALM Buoy
The company receives a contract for the first deepwater CALM buoy, Girassol.
1996
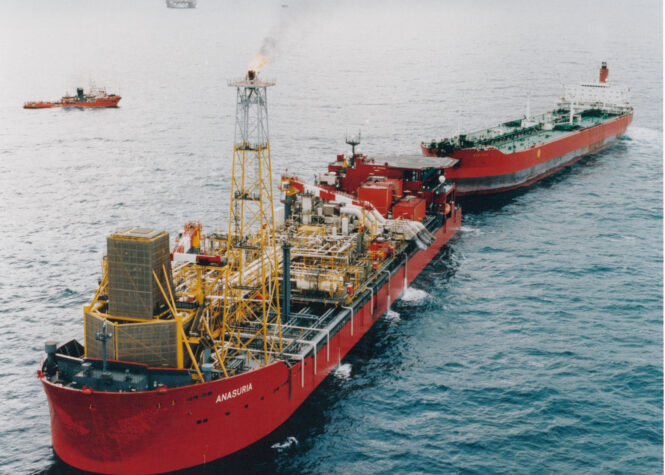
Turnkey North Sea FPSO
Delivery of a newbuild FPSO (Anasuria) for Shell on a fixed-price turnkey basis.
1993
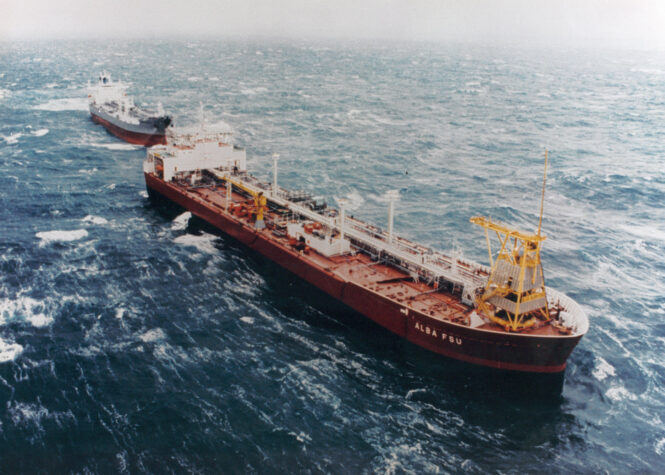
North Sea Internal Turret
The company supplies the internal turret for the first permanently moored tanker in the North Sea for the Alba field, UK.
1990
Acquisition of IMODCO
IHC Caland acquires the California-based company IMODCO, SBM’s largest competitor in the supply of single point mooring systems.
1988
MSC Rejoins the Group
MSC (the engineers who left Gusto Engineering in 1978) are reintegrated back into the Group.
1986

Disconnectable Turret
The first disconnectable turret system is installed on the Jabiru field, Australia.
1985
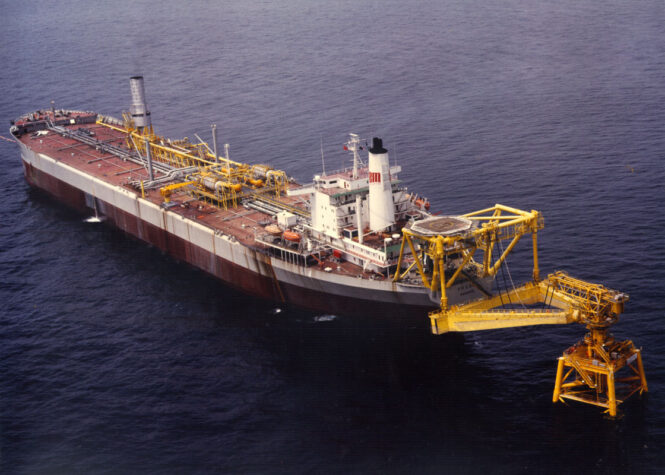
Jacket Soft Yoke
For shallow water projects, the soft yoke mooring system replaces the SBS (Single Buoy Storage) system in many applications. Used in combination with a fixed jacket structure, production flows through steel pipe risers.
1985
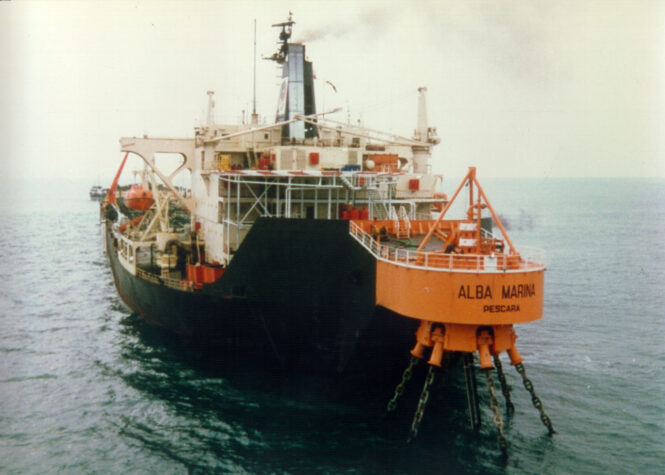
External Turret
The use of mooring systems in increasing water depths facilitates the move to tanker conversion via an external turret as a replacement of the Single Buoy Storage systems.
1981
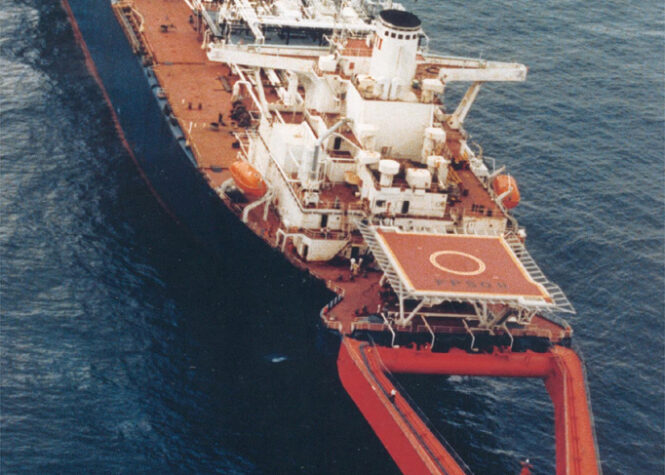
Leased FPSO
FPSO II, the first leased floating production system starts operations on the Cadlao field in the Philippines.
1978
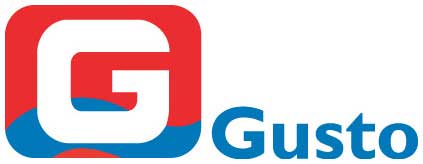
Gusto Engineering
After the closure of the Gusto shipyard in the 1970s, the decision is made to retain the engineering expertise and experience of the company with the creation of Gusto Engineering. Some of Gusto’s original engineers opted to form another independent company under the name Marine Structure Consultants (MSC) and specialize in jack-up technology.
1977
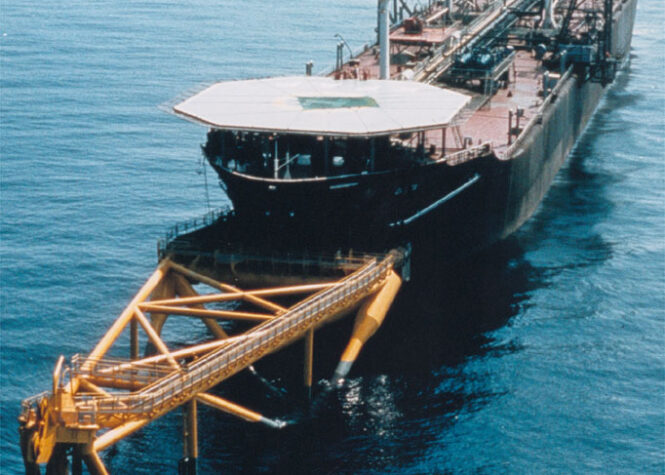
SALS Mooring System
SBM develops the SALS (Single Anchor Leg Storage) yoke to eliminate the need for dynamic risers required for the typical CALM system, and to maximize production uptime through a permanent mooring on the site of the FPSO.
1974
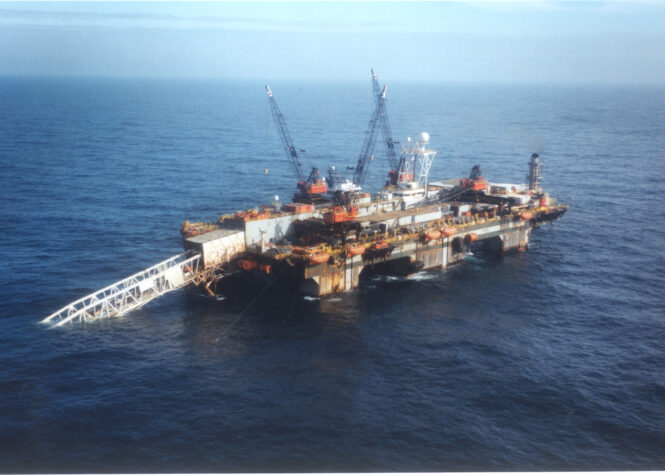
Semisubmersible Pipelay Vessel
The world’s first semisubmersible pipelay vessel, the Viking Piper, is delivered. The Viking Piper, now the Castoro 7, was considered to be the frontrunner of the third generation lay barges.
1973
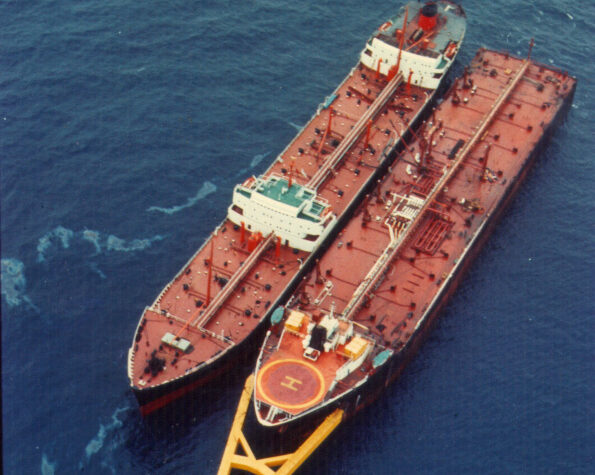
SBM Mooring System
SBM designs the first permanent mooring system when the Ifrika SBS was commissioned for Elf’s Ashtart field off the Tunisian coast in the Mediterranean.
1972
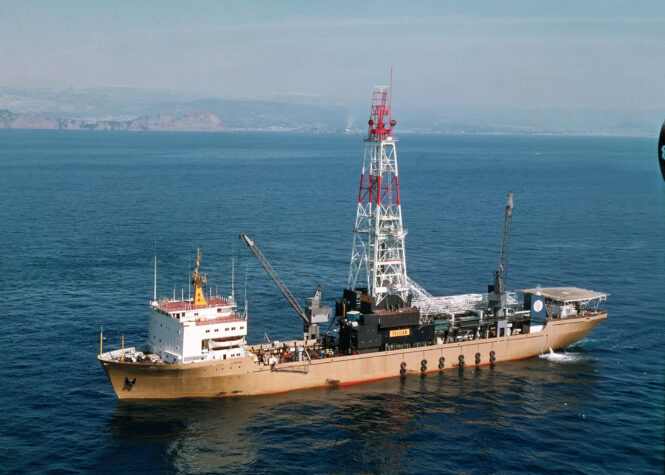
DP Drillship
The first dynamically positioned drillship unit was delivered (development began in 1969). The Pelican class of DP drillships, some of which are still operating today, is well known in the industry.
1969
SBM Inc. established in Switzerland
The market for SPM systems develops quickly, expanding to near-shore tanker loading and discharge and offshore oil fields. As these systems have a different clientele that require different technologies than the standard technologies of the Gusto yard, the decision is made to create a separate company for the marketing and further development of SPM systems. Single Buoy Moorings Inc. (SBM) is founded as a wholly owned subsidiary of IHC Holland, N.V.
1960
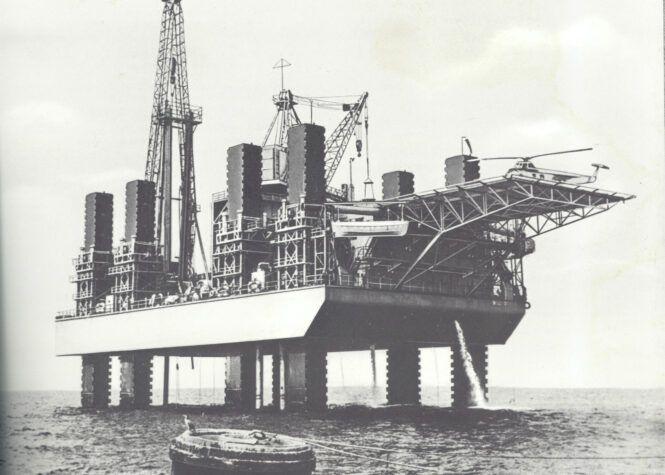
Drilling Jackup
The Shell relationship developed during production of the first CALM Buoy, leading to the design of the first jackup drilling rig, the “Seashell.”
1959
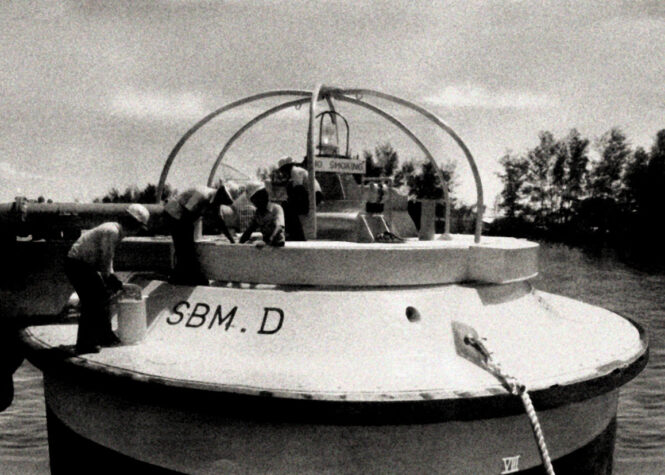
CALM Buoy
Gusto Shipyard constructs the first Single Point Mooring (SPM) facility under a license agreement with Shell.
1905
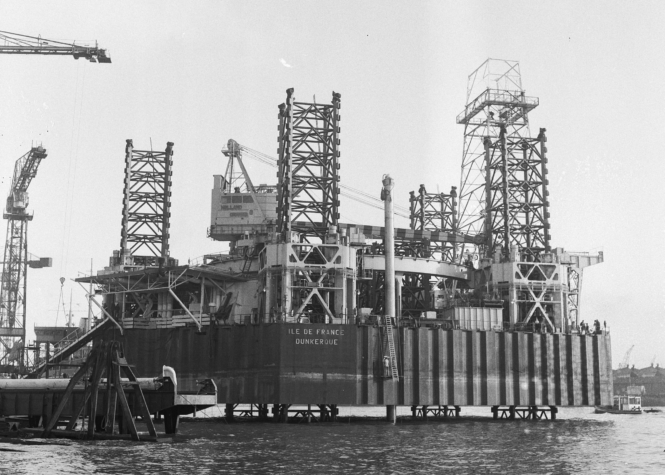
Birth of Gusto Shipyard
The Smulders Machine Factory purchases a plot of marshland in Schiedam, The Netherlands, for new facilities. The relocated company is named “Werf Gusto.” Before construction of the facilities begins, the site is raised four meters. The Gusto yard, with its state of the art facilities, has a direct link to the North Sea.
1862
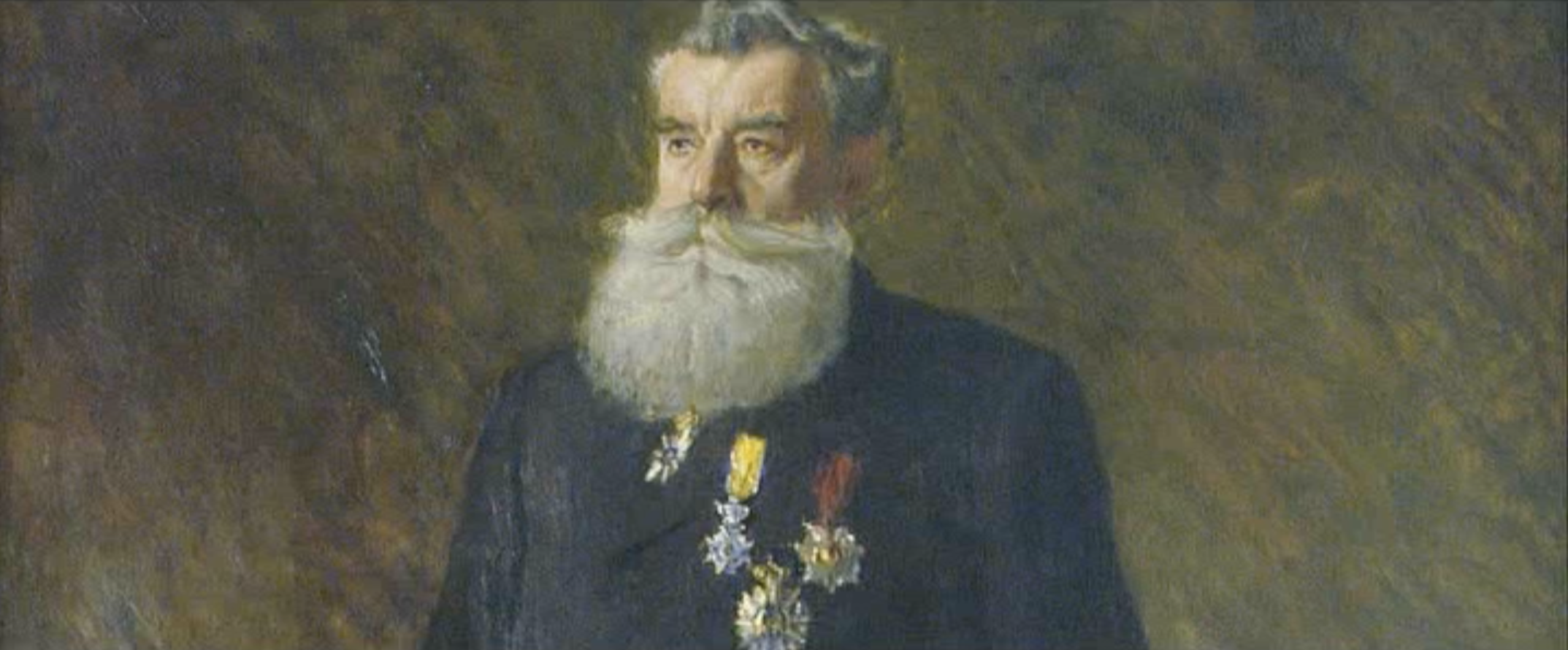
A.F. Smulders Machine Factory
Entrepreneur A.F. Smulders starts his own factory, specializing in steam engines and boilers, before diversifying into an iron foundry.